Case study - New Lynn to Avondale shared path
- Sarah Farr
- Jan 21
- 3 min read
Updated: Jan 21
Timeframe:
14 day firm deadline, 26 December –9 January to accommodate a block of line. Project completed 2 days early.
Identified issues:
The train line had to be up and running by the end of the holiday period.
Tight timeframe, 24-hour continuous work required to deliver within a non-negotiable two-week period.
No float in the programme, meaning there was no extra time that could be allowed.
Benefits of having Hoffcon on the job:
Our construction method and temporary works design meant that the underpass construction could happen in the required two-week period.
Our project management approach optimised coordination which meant the underpass construction was completed 2 days ahead of time on a planned programme of 14 days. This equates to 14% time saved. The train line opened before the end of the holiday period, making the client very happy.

Overview:
As part of the New Lynn to Avondale Shared Path project, the underpass install involved significant planning and coordination as the rail line had to be stopped while the underpass was completed. It was important to select the right off-peak time period that caused the least disruption to the public and other stakeholders while balancing the need to deliver the underpass on time. The construction happened over the Christmas holiday break.

Approach:
Dempsey Wood engaged our services to design temporary works and create the construction methodology and programme for the underpass works. Given the various risks and tight time constraints, Hoffcon was called on, as managing director and founder, David Hoffman (aka Hoff), has a huge amount of experience in match-casting segmental construction. The project team saw this methodology as key to delivering the job successfully.
We created the method statement that outlined the step-by-step tasks for delivery. This included designing the temporary stressing arrangements that hold the units together. Hoffcon's process for developing method statements includes full geometry checks to ensure the units wouldn't clash. We also check to make sure materials and plant used to perform the tasks are ordered at the right size and quantity, reducing site rework. This care and attention to detail was appreciated by the site team and made setting up on site easy.
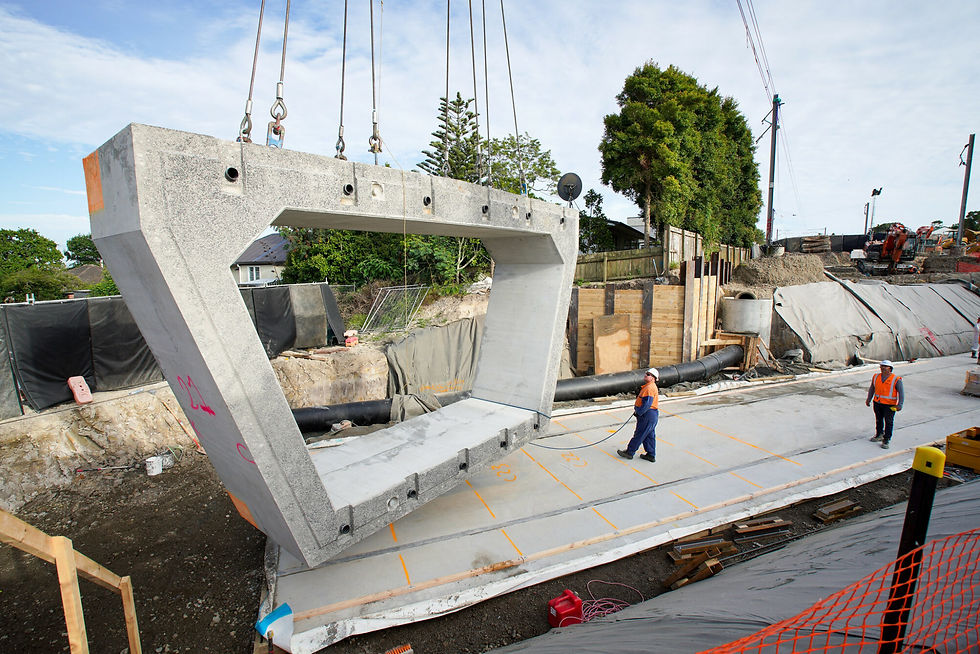
Project management:
Hoffcon created the programme and quality tasks for the underpass construction. Based on the tight timeframes and need for tight coordination, we configured a cloud and mobile-based tool so coordination could happen in real time.
This meant:
coordination was optimised; if any part of the project was ahead of schedule, contractors were able to come in earlier than originally planned.
parties could upload quality documentation directly from site as works progressed and get reviews or hold points released by others without delay.
the client had visibility of progress in real time to give them confidence the work was on track over the Christmas period.
project leads were able to work remotely without affecting delivery as they had access to what was happening on site at all times of the day.
We itemised all requirements of the project down to the hour, scheduling the various subcontractors so they knew exactly what they needed to do and where they needed to be at any time. Hoffcon ensured all necessary personnel were trained in the systems to avoid any hold-ups and we were on call during construction to ensure everyone had the training and tools they needed.
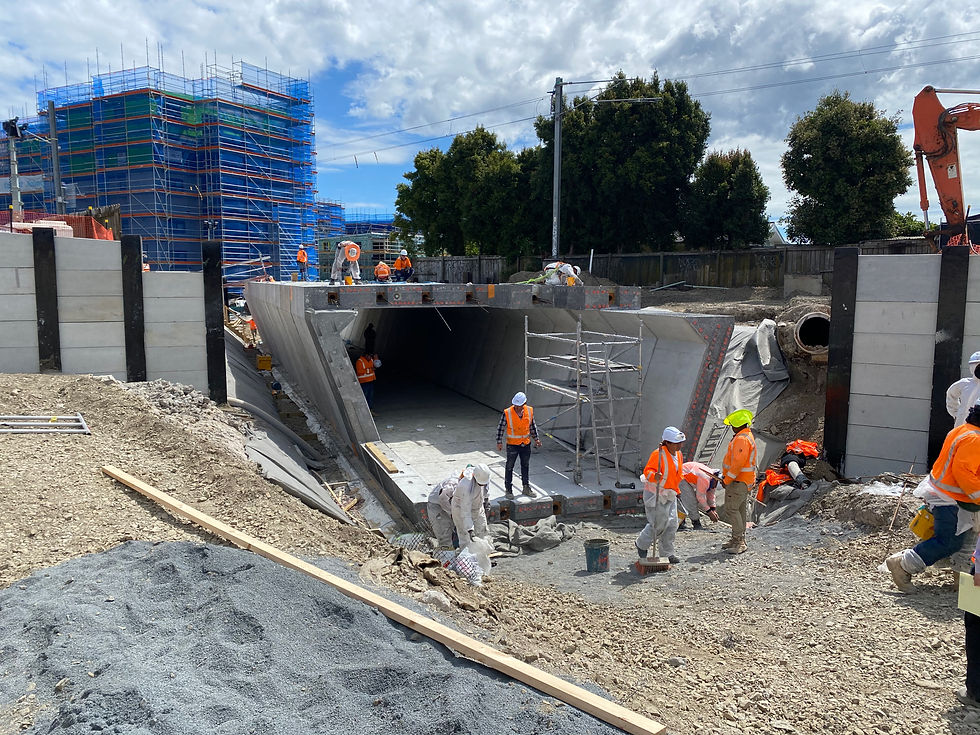
This dispersed and system-based way of running a project isn't new for Hoffcon; it's our way of working. We have a dispersed team throughout New Zealand and operate in a completely digital way. We want to show other construction and engineering organisations that tying in good process with cloud-based and mobile-friendly systems makes construction faster, simpler and reduces administration, and this job absolutely proved that.
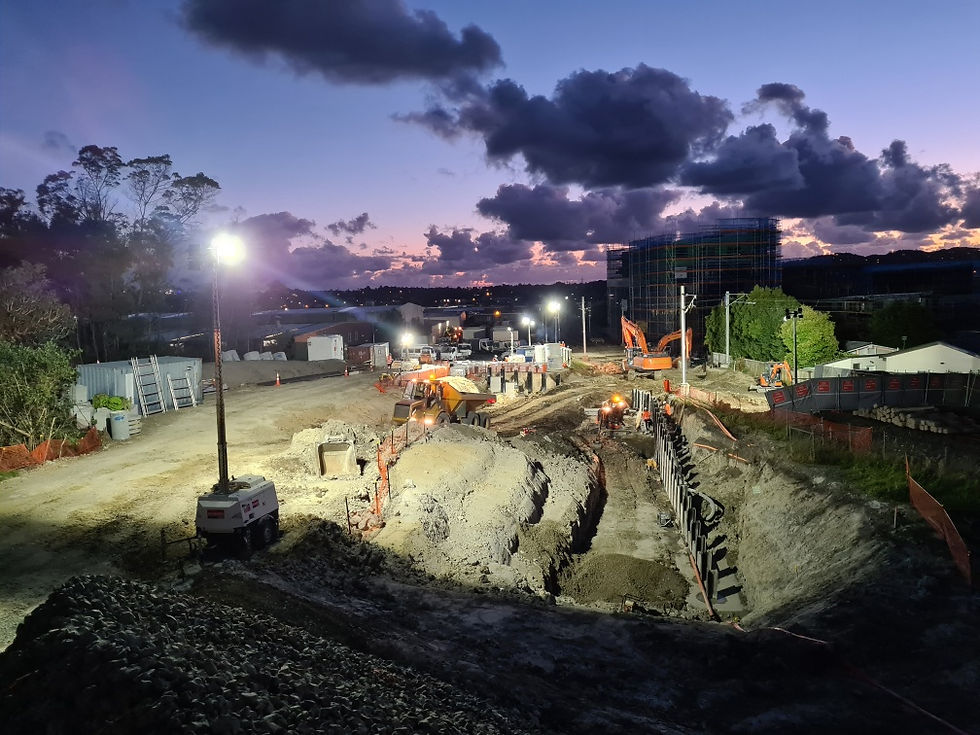